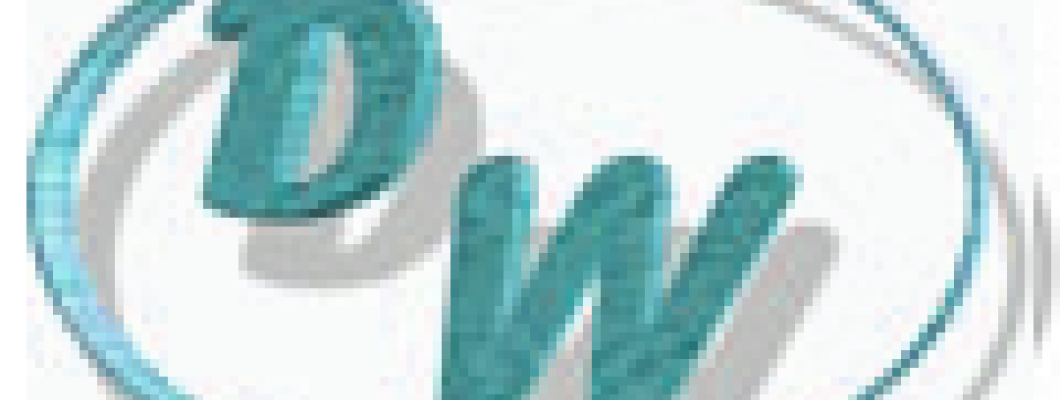
DW Mouldings invests in top of the range machinery
Demand for DW quality mouldings and flooring has necessitated the investment in a third Weinig Powermat moulder, the first UK company to have three of Weinig’s top of the range Powermat moulder models – two Powermat 3000 fully automatic computerised machines and a Powermat 1000. All three moulders have PowerCom quick set-up facilities and the back-up of a state-of-the-art toolroom: with HSK PowerLock tooling; OptiCom computer setting and tool management system; two Rondamat 960 grinders and a computerised template maker.
Not so long ago, D W Mouldings Ltd, of Sandy, Bedfordshire, had eleven conventional moulders – now they have just four, and 99% of the work is done on the three Weinig’s. With a lot fewer operators and more floor area to accommodate work in progress, the company production throughput has increased to meet demands and provide spare capacity for further growth. High-quality finish was always their claim, but now they achieve it with faster feed speeds, minimal downtime and quick changeover times.
With conventional moulders, the average job changes they achieved per day was four. Now on an average day, they change over 10 to 12 jobs and, when they have a lot of short runs, they can do up to 25. Customers often remark on the quality and speed of service.
“Before we invested in our first Weinig Powermat 3000, we were sceptical that it could replace three conventional moulders”, says Brian Dossett, Chairman of DW Group. “We were also concerned about what would happen when it ‘went down’. But we were soon convinced that the new Weinig technology was the way to go, thanks to the reliability of Weinig’s engineering and back-up service”.
“The three Powermats are providing excellent benefits”, adds David Howard, Managing Director of D W Mouldings Ltd. “I particularly like the PowerCom quick setting feature, the faster throughput at 12,000rpm cutter speeds and the super finish achieved by the HSK PowerLock tooling at the higher speeds. The technology will meet our needs for the foreseeable future”.
Using patented PowerLock HSK tooling
The heart of the Powermat moulding system is the patented PowerLock HSK tooling which incorporates the spindle into the cutterhead. It’s light and easy to use and is changed in seconds at the press of a button. No spindle. No spacers. No spindle nut. No wrenches. And no possibility of mistakes. With cutterhead speeds up to 12,000rpm it doubles the feed rates in comparison to conventional moulders.
The PowerCom system offers the advantages of a memory system plus almost unlimited memory for profiles and tooling measurements. With the easy-to-use touch screen, you are guided through every decision. Enter the tooling measurements and the dimensions of the profile, and the PowerCom software calculates where the cutterheads should be positioned, and displays this on an electronic readout.
The tool room at D W Mouldings is very important for ensuring tooling management and record-keeping for quick and easy access of information – particularly for re-runs. The key toolroom feature is the OptiCom measuring stand which serves all three Weinig Powermat's and ensures the first piece through is perfect with minimal set-up time on the moulder. DW also has two Rondamat 960 profile grinders and a computerised template maker in their toolroom.
The DW Group
D W Mouldings is part of the DW Group of Companies with their headquarters in Tottenham. Their Tottenham factory, DW General Wood Machinists Ltd, established in 1948, also has a substantial size wood mill and showroom. They complement each other, with DW in Sandy focusing on mouldings and the Tottenham factory producing a wide variety of products – from components for Formula 1 wind tunnels, parts for underground trains, point of sale displays and products for the gaming industry. In fact, anything a customer may request.
DW in Sandy, established in 1971, is a specialist hardwood timber merchant, timber supplier and wood moulding mill. The latter is the fastest growth activity, hence the heavy investment in the latest technology.
DW stock and supply North American and European temperate hardwoods including Oak, Ash, Maple, Cherry and Beech, and also various species of tropical hardwoods, including Sapele, Iroko, Meranti and Seraya. All their timber is purchased from approved sources and when necessary FSC, PEFC & MTCC certified.
Their customers, who comprise contractors, shopfitters, Flooring companies, builders, carpenters and joiners, can be provided with any moulding profile and if required, primed and lacquered with water-based products, in their in-house finishing line. Quality of finish is guaranteed, and short-run orders are just as easy to meet, as long runs.